A recent survey revealed that one of the most common Quality system issues that Australian contractors has is the struggle to get subcontractors and engineers to write 'good' ITPs.
Our Board spent some time coming up with the following introduction for the industry - hopefully it will provide some guidance for people creating ITPs for the first time.
Thanks to Mark Hamilton and Greg Wennerstrom for their additional contributions.
Updated 21/01/2025 to refer to standard template - access to CQA members only.
Introduction
What is an ITP?
An Inspection & Test Plan (ITP) is a document that is created on a Construction Project which details the “plan” for managing the quality control and assurance of a particular element of the construction works.
It is a comprehensive list of inspections and tests that need to be undertaken to ensure the quality of the delivered works - providing details of the requirements, an overview of the method(s) to be used, responsibilities of relevant parties (including agreeing Hold Points and Witness Points), and any documentary evidence to be provided to verify compliance.
Agreeing these Inspections and Tests between all the parties ensures that there is clarity and alignment on requirements – and therefore no surprises.
Here is an example of an ITP:
Who creates ITPs?
Depending on the nature of the work and the contractual arrangements, ITPs are typically either created by the Subcontractor or the Head Contractor responsible for the works.
What template should I use?
ITP-creators may be required to use a Client template, a Head Contractor template – or they may use their own.
CQA Members may use the standard ITP/ITR Template which is available in the member's area:
It’s much simpler to review and use ITPs with a simple consistent template – standards are therefore mandated on many projects.
It is also becoming commonplace for project to digitise ITPs into project digital systems – in this case, a standard template is necessary to simplify the upload process.
Note that there are two types of ITP template (and process):
ITPs that also serve as the checklist – these are designed and structured to be progressively signed-off for each element of works that they relate to.
ITPs that contain the plan of works and reference Inspection and Test Reports (ITRs) – these are designed to be signed off in separate ITRs for the activity
Rail projects may require a place in the template to reference particular Inspections or Tests to the project Requirements Matrix.
Using ITPs
How are ITPs used?
Once the ITP is developed, it is typically reviewed and approved by a technical person (who this is will depend on your project) prior to being Approved for Use.
Once it is approved, the contents of the ITP are then briefed out to the team doing the work.
Tests and inspections are completed in line with the ITP, records are kept, and the ITP is “signed-off”. As we described above, there are different ways in which the ITP can be “signed-off” – on the ITP itself or on a related ITR (in paper copy or in digital format). In either case, the work needs to be progressively signed-off as the works is done.
Any nominated Hold Points may be signed-off on ITP/ITR itself or digitally in the project’s Electronic Document Management System (EDMS).
When the element of work and ITP/ITR relating to it is complete, the ITP/ITR and any associated records are then stored in the project’s Electronic Document Management System (EDMS) as a record of the works.
Developing the ITP
1. Determine the requirements for the activity
The first step of developing an ITP is to understand the requirements for the activity.
An ITP should only cover one activity – the more technical aspects that are included in a single ITP, the more difficult it will be to get it signed-off.
The basic requirements for the ITP are contained in the Project Specifications – although based on the nature and type of your project, there may be requirements in your contract, your Scope of Works and Technical Criteria, and/or Design Drawings. You may even have to review relevant Australian Standards.
Seek out knowledge on your project and with your stakeholders (designers/clients/subcontractors) – consult with your company's technical Subject Matter Experts. Are there any common quality risks or issues which are not covered in the project technical documents that you need to consider in the ITP?
Organise a short kick-off meeting on Teams or Zoom with your stakeholders to discuss the requirements and controls - ensure that you understand their concerns and the intent of their controls.
Sometimes other non-technical approvals may be pushed into the ITP – like pre-works environmental approvals – this is not the core purpose of the ITP, but it may assist with confirming that these aspects are signed-off.
Gather these documents together and extract the requirements for your ITP – these may described as:
an end state (eg a statement of flatness or of hardness)
the outcome of the application of a test method or an inspection outcome
2. Sequence the activities into Preliminary Approvals and Construction Activities
Now you understand your technical requirements, you can create your draft ITP.
First lock in the next sequential number from your Document Controller or Quality Manager - then list the relevant technical references (i.e. specifications and Australian Standards) to your ITP (many ITP templates have a section for this on the first page).
Many larger engineering organisations create Construction- or Work- Method Statements to document the whole plan of works - including all activities. These are a useful source to help sequence the activities in your ITP.
An ITP is always sequential – the list of tests and inspections in the ITP should mirror the real-life sequence of tests and inspections. However, the bigger the ITP, the more difficult it is to compile and to complete. The best ITPs are broken-down or structured so that they can be completed in manageable chunks.
For a steel fabrication package, this might be:
Master ITP (one-off activities such as materials approvals which apply cross-package)
Fabrication ITP (tests and inspections undertaken by the fabricator – per fabrication lot)
Installation ITP (tests and inspections undertaken for each steel installation)
For a concrete package, this might be
Master ITP (one-off activities such as mix-design approvals which apply cross-package)
Installation ITP (tests and inspections undertaken for each concrete pour/area)
You could have one massive ITP – but as there’s normally a one-to-one relationship between the ITP and the Lot (the record-set for the contents of the ITP) this will make it extremely difficult to close out work.
3. Provide the control detail for each individual item on the ITP
This is where the detail comes in – for each of the activities you sequenced in the previous section, you now need to provide:
Specification Reference – this references the clause of the Spec (and the specification itself if you have multiple specs in the same ITP)
Method – this describes the type of test activity which is applied – based on your company and project requirements this could be a simple description (such as Visual Inspection) or could be a more detailed description of a test method.
Acceptance Criteria – this describes the specific outcome which must be met for this line item to pass (putting “refer to spec” in this column is lazy ITP writing and makes it more difficult to confirm compliance)
Frequency – is this activity undertaken for 100% of the Lot, only a proportion of the lot, or only one lot in several?
Verification Details – is the requirement to execute the test or activity, or is there a requirement for external inspection/witnessing via a Hold/Witness Point?
Responsibility – who is responsible for undertaking this activity? Is it the Subcontractor, Head Contractor, Consultant, Client?
Record – what is the required output of this activity? Is it a Report, or a sign-off on a checklist?
4. ITP Review and Approval
4.1 Review for Nominated Authority/Client Hold and Witness Points
Once drafted, ITPs should be formally issued via the project EDMS to nominated authorities such as Design Consultants and Clients – so that they can confirm/add Hold and Witness Points.
4.2 ITP Approval
Once created, ITPs need to be issued via the project EDMS for approval. Depending on your company and Client requirements, this may be approved by the Client.
As a minimum, ITPs should be reviewed internally on the project – and then issued to the Design Authority for review.
Some systems require ITP Templates to be signed to indicate approval.
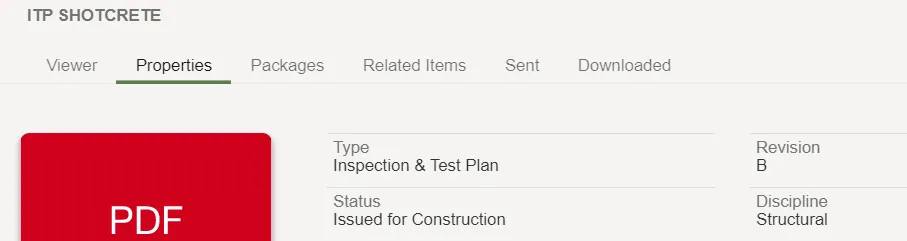
image of an Inspection and Test Plan in Aconex Documents
5. Template ITP Storage
Now you have an approved Template ITP for your activity, this needs to be uploaded as an approved controlled-document in your EDMS (this step may have already been achieved through your review and approval process).
The approved ITP template must be transmitted to all the interested parties (consultants, subcontractors) so that they are aware of what has been agreed.
6. ITP Briefing
It is good practice to brief out the relevant requirements of the ITP to your project team and the workforce – and keep records. Make sure that people understand their role, and the requirements for Hold and Witness Points.
If you have any feedback, please respond to this guide so we can improve it - if you like it, please share it!
Comentarios